L’usine du futur de BCG a accueilli notre suite logicielle MES
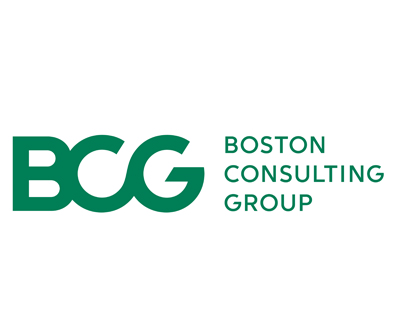
Le Cabinet international de conseil en stratégie, Boston Consulting Group (BCG) a choisi VIF pour rejoindre l’écosystème des fournisseurs français sélectionnés dans le cadre d’un projet ambitieux : un centre d’innovation pour les opérations. Cette usine modèle est un projet mené sur 5 ans afin de mieux comprendre les concepts de l’industrie 4.0 pour les mettre en œuvre efficacement. Immersion au cœur de l’ICO…
Usine du futur…L’ICO du BCG
L’ICO (Innovation Center for Operations) est né en région parisienne, en octobre 2016, dans l’Essonne, à Villebon-sur-Yvette. Cette usine imaginée, conçue et gérée par BCG reproduit des lignes de production réalistes, très complètes qui fabriquent de vrais produits. On assemble des scooters, des appareils ménagers et on produit des bonbons. C’est sur cette dernière ligne, dédiée aux industries de process et de conditionnement, que VIF a intégré, depuis un peu plus d’un an, ses solutions logicielles MES.
La suite MES permet un pilotage en temps réel grâce à des données de plus en plus fiables et pertinentes car en lien avec l’utilisateur et son environnement de travail.
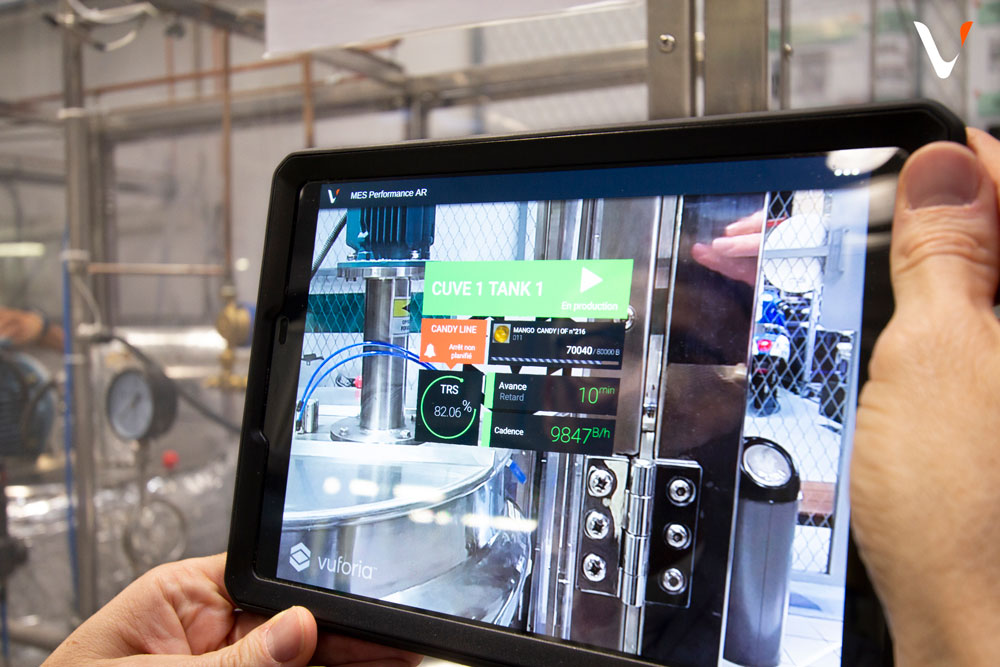
Des technologies au service de la compétitivité industrielle
L’ICO offre un potentiel d’expérimentation inédit. Le BCG a déployé huit grandes familles de technologies : robots et machines collaboratives, cloud, simulation, fabrication additive, Big Data, Réalité Augmentée, Réalité Mixte, cybersécurité, solutions d’optimisation et IIOT.
Pour chacune de ces technologies, BCG a fait appel à des fournisseurs français aux savoir-faire innovants.
Nous avons créé une solution de réalité mixte connectée en temps réel avec la suite MES compatible avec le casque Microsoft HoloLens mais surtout avec n’importe quel smartphone et/ou tablette, solution qui permet à l’opérateur et/ou au superviseur d’accéder à l’information qui l’intéresse, au bon endroit et au moment le plus approprié. Concrètement, le superviseur voit ses indicateurs à travers le casque, en mobilité et en temps réel, l’état de chaque machine et l’avancement de sa production.
Pas de révolution du parc machines
Il est possible de faire entrer la dimension 4.0 à des endroits précis de la chaîne de fabrication, en intégrant par exemple, une solution comme le logiciel MES, en ajoutant des capteurs traditionnels, ou en s’appuyant sur la technologie des IIOT.
Nous pouvons ajouter du “4.0” sur l’existant. C’est le cas, sur la ligne de fabrication de bonbons, puisque notre solution de réalité mixte se base sur un environnement et des équipements qui ne sont pas de nouvelle génération. Son installation est rendue facile par l’utilisation de tablettes standards et de simples marqueurs à poser sur les machines.
Reproduire les problèmes quotidiens pour les solutionner.
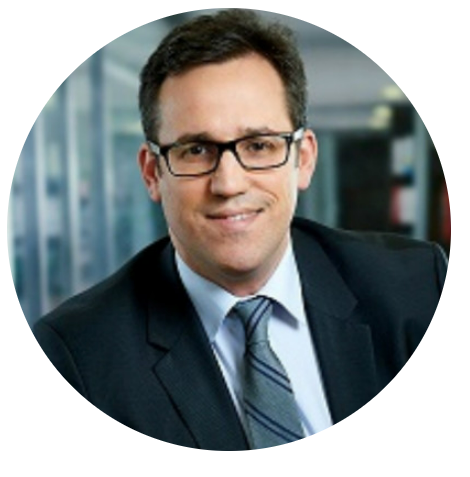
Moundir RACHIDI
directeur associé du cabinet bcg en charge des opérations
» L’idée n’était pas de présenter une usine totalement 4.0, car cela n’aiderait pas les industriels à se projeter, mais bien de reproduire les problèmes auxquels sont confrontés les industriels sur le terrain et de proposer une manière de les résoudre »
Trouver des solutions répondant à des problèmes techniques, organisationnels ou directement liés aux ressources permet de gagner en performance et en productivité dans un contexte industriel de plus en plus complexe.
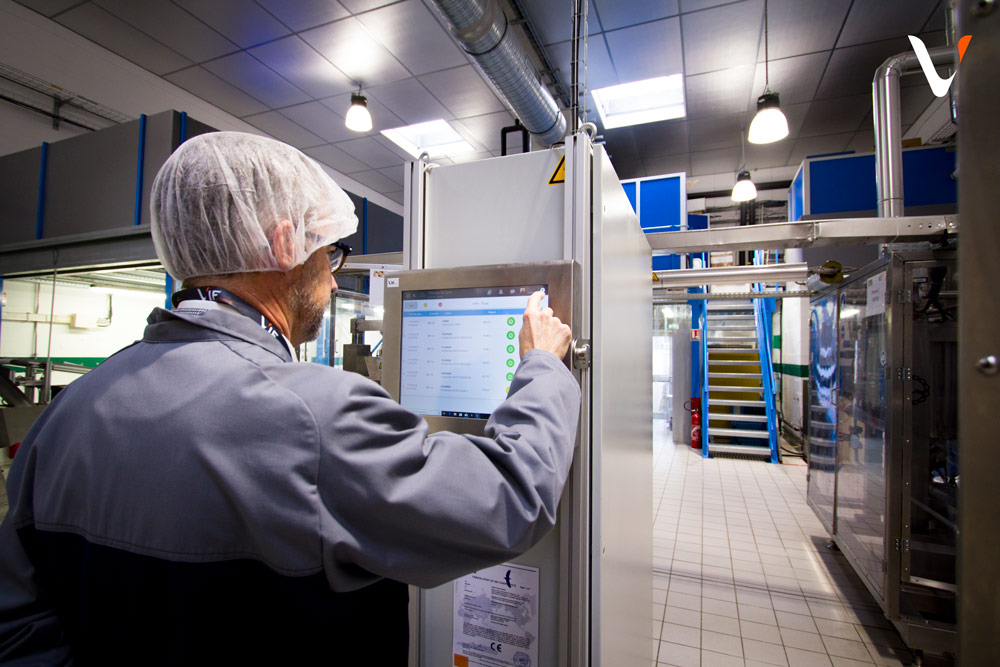
L’humain au coeur des technologies
Qui dit usine du futur peut faire penser à une usine sans présence humaine, connectée et robotisée : il n’en est rien !
Déployer des outils, des solutions, développés sur la base de des nouvelles technologies et les associer aux organisations, aux process et aux équipes est un vrai challenge qui apporte alors de véritables contributions sur le plan humain : plus d’autonomie, plus de sens au travail, plus d’échanges, plus d’attractivité.